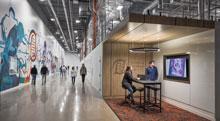
Navigating the Challenges of Advanced Manufacturing Facility Planning and Design
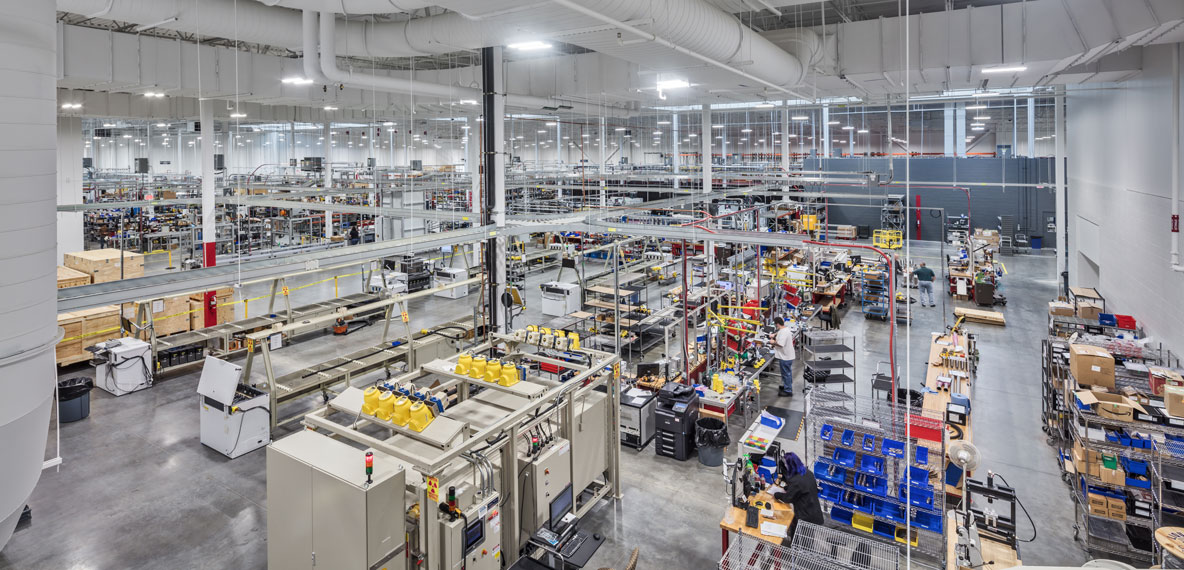
For years, industrial companies have grappled with the complexities of planning, designing, and executing advanced manufacturing facilities. This intricate process has been further complicated by challenges facing industrial real estate today. Industry leaders gathered at the recent IAMC Fall Forum in Quebec City to discuss many of these pressing issues.
A critical topic at the forum was the ongoing global disruptions impacting supply chains. With the historical offshoring of production, accessing raw materials has become increasingly difficult. This issue is compounded by the logistical strain of last-mile delivery, particularly in the context of global trade dynamics.
Moreover, attracting and retaining skilled talent poses a significant challenge. As noted in discussions at IAMC, the demand for skilled workers is growing, especially in the industrial and manufacturing sectors. Operating high-speed production lines requires individuals with specialized training and expertise, and finding and retaining such personnel in a competitive labor market adds another layer of complexity.
Finally, the rise of e-commerce was another focal point at the forum, with industry leaders discussing how consumer expectations have transformed industrial real estate. The need for larger, strategically located logistics hubs and distribution centers to support faster delivery times is now a primary consideration.
In response to these challenges, companies must take a strategic approach to ensure long-term success. By addressing supply chain resiliency, talent retention, and the demands of e-commerce, industrial firms can build more adaptable and sustainable operations. Below are several ways to approach these obstacles effectively.
Approaching These Challenges
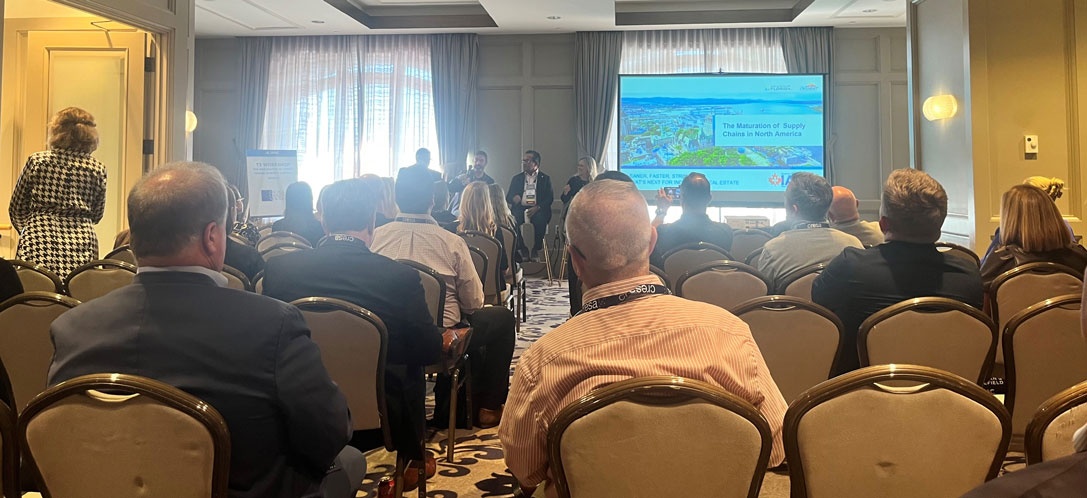
At the IAMC Fall Forum, “The Maturation of Supply Chains in North America” offered insights into current onshoring and nearshoring trends.
- Ensuring Supply Chain Resiliency: Global supply chain disruptions have pushed manufacturing companies to reassess their production strategies. Much like the onshoring and nearshoring trends highlighted in “The Maturation of Supply Chains in North America,” led by Meghan Case, Jorge Ojeda, and Felix Tejeda, companies are seeking ways to bring operations closer to home. This shift is driven by the need for shorter, more controllable supply lines, reducing dependence on long-distance logistics that can be vulnerable to global crises. A 2021 survey indicated that 83% of manufacturers were likely to reshore, a significant rise from 54% in the previous year, underscoring the urgency of this trend. In response, manufacturing construction in the US has surged, particularly in the South, where investments reached $108 billion between March 2023 and March 2024. BHDP recommends creating 10-year master plans for each site, as well as how each site works together towards the company’s goals.
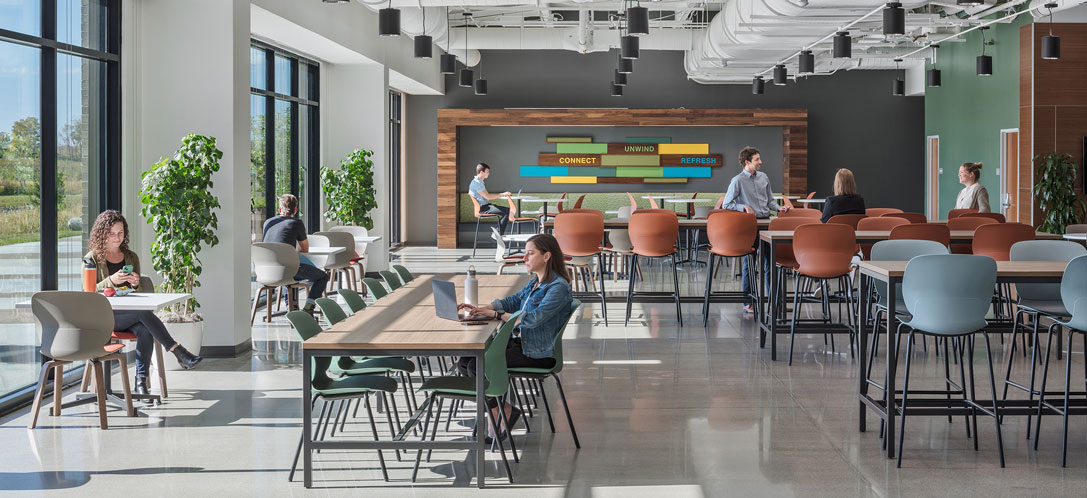
Inside VEGA's new North American headquarters, a strategically located café has direct access to natural light and boasts a calm, quiet environment. View the VEGA Project Story
- Attracting and Retaining Talent: To attract and retain top talent, it’s essential to integrate amenity-rich spaces within manufacturing facilities. Discussions at IAMC explored how companies can create more engaging work environments, incorporating amenities and spaces that foster employee well-being. Early in the design process, involving employee focus groups to gather input on desired amenities—such as comfortable break areas, fitness facilities, and outdoor spaces—can help ensure the environment meets the team's needs. Features like good air quality, natural light, and biophilic elements, such as views of the outdoors or access to walking trails, not only improve employee health and satisfaction but also foster creativity and collaboration. Calm, uncluttered areas for respite, like cafes or break spaces, empower employees to disconnect during breaks, which reduces stress and fatigue, ultimately boosting productivity.
- Adapting to the Growth of eCommerce: The rapid rise of eCommerce has transformed consumer expectations, pushing companies to expand their warehousing and supplier networks to meet the increasing demand for faster delivery. This shift underscores the need for strategically located production and distribution facilities to support quick delivery times while enhancing supply chain resilience. As businesses strive to remain competitive in a fast-evolving market, the demand for larger, more efficient logistics hubs and distribution centers continues to grow. To navigate these challenges, BHDP helps clients take a long-term, strategic approach by master planning for the next 10 years. This allows businesses to evaluate current operations, forecast future needs, and ensure their facilities are scalable, adaptable, and sustainable. By optimizing site layouts and integrating technology, companies can reduce operational risks and make informed decisions about expansions while staying aligned with business goals and customer expectations.
The Need for a Strategic Partner
The IAMC Fall Forum underscored the importance of adaptability, collaboration, and strategic planning as we move forward in a rapidly evolving global landscape. Partnering with an experienced firm can provide invaluable support in addressing these challenges. BHDP leverages a proven design process and a collaborative team to ensure that the manufacturing facilities we design are equipped to meet present demands and primed for future growth.
A holistic approach to facility planning involves understanding long-term objectives, translating them into actionable plans, and optimizing equipment layouts for maximum efficiency. This strategic foresight enables companies to future-proof their operations while maintaining business continuity.
Successful advanced manufacturing facility planning and design requires a blend of foresight, expertise, and collaboration. By embracing these principles, companies can navigate the complexities of the modern industrial landscape and position themselves for sustained success.
Looking for a strategic partner to help plan, design, and execute an advanced manufacturing facility? Complete our contact form today.
Author
Content Type
Date
October 04, 2024
Market
Practice
Topic
Manufacturing Equipment
Innovation